© Альтшуллер Г.С., Шапиро Р.Б. Научный и производственный бюллетень «Кислород» Главкислорода Министерства химической промышленности СССР. – М. - № 6. (декабрь) – 1950 г. – С. 36-40.
ХИМИЧЕСКИЙ АППАРАТ ДЛЯ ПОЛУЧЕНИЯ КИСЛОРОДА
Автогенная сварка и резка металлов находит широкое применение при ремонтных работах. В большинстве случаев эти работы могут быть выполнены с использованием обычных ацетиленовых генераторов и кислородных баллонов. Однако существуют ремонтные и монтажные работы, для которых применение обычной аппаратуры весьма затруднительно. К таковым относятся непродолжительные ремонтные работы, производимые в удалении от баз или в сложных местных условиях (например, в гористой местности). В этих случаях использование громоздких ацетиленовых генераторов и тяжелых кислородных баллонов не только не рационально, но иногда просто невозможно.
Поэтому уже полвека назад были предприняты попытки сконструировать портативный химический кислородный генератор для производства небольших сварочных работ. Одним из пионеров в этой области был известный русский авиаконструктор Н.П. Лобанов. Изготовленные по его предложению кислородные генераторы, работающие на патронах из бертолетовой соли, применялись русскими войсками в период первой мировой войны.
В последующие годы выпускались аппараты, получение кислорода в которых основано на реакции между перекисями или четырехокисями щелочных металлов и водой.
Оба эти типа аппаратов не получили широкого распространения и постепенно были забыты. Это объясняется в первую очередь их недостатками, обусловленными выбором исходного вещества в качестве источника получения кислорода.
В настоящее время, когда автогенная сварка применяется очень широко, вновь становится актуальной проблема создания портативного химического генератора для получения кислорода, дающего возможность проводить небольшие по объему сварочные работы.
Горючим для сварки в этих условиях могут служить пары бензина. Портативная аппаратура для их использования уже существует и задача, таким образом, сводится к комбинации двух приборов — кислородного генератора и бензобачка.
Технические требования к генератору кислорода определяются, с одной стороны, необходимостью сохранить портативность прибора, а с другой — получить достаточный запас кислорода.
Учитывая вес бензобачка, горелок, шлангов, вспомогательной аппаратуры, инструментов, следует принять для кислородного генератора максимально допустимый вес не выше 8—10 кг [1]. Запас кислорода должен составлять не менее 200—300 л при давлении 3—10 атм. и производительности до 1,2—1,5 м3/час.
Кроме того, к кислородному генератору должны быть предъявлены общие требования для таких аппаратов: максимальная простота устройства, надежность, удобство и безопасность в эксплуатации и т. п.
ВЫБОР ИСТОЧНИКА ПОЛУЧЕНИЯ КИСЛОРОДА
Выбор того или иного источника получения кислорода является основным фактором, определяющим конструкцию генератора.
Ко всякому химическому соединению, используемому в качестве источника, получения кислорода, должны быть предъявлены следующие требования: высокое содержание активного кислорода; легкость выделения кислорода; равномерность выделения и возможность простой регулировки процесса (включая и остановку его); полнота выделения кислорода; безопасность; удобство транспортировки и хранения; экономичность.
Бертолетова соль и перекиси щелочных металлов не отвечают всем перечисленным требованиям.
Раз начавшееся разложение брикета бертолетовой соли нельзя остановить, как нельзя изменить и скорость разложения. При ремонтных работах, когда приходится часто выключать горелку, неизбежны значительные потери кислорода. Разложение брикетов, особенно хранившихся длительное время, происходит неравномерно, поэтому изменение количества подаваемого кислорода отражается на качестве сварки. Если же применять редуцирующие приборы для устранения колебаний давления газа, то это вызовет значительное усложнение прибора.
Скорость реакции между перекисями щелочных металлов и водой в значительной мере определяется внешней температурой. При низких температурах, вследствие возможности замерзания воды, использование этой реакции вообще невозможно.
Со многими органическими соединениями перекиси металлов образуют вещества, взрывающиеся иногда даже от тепла, выделяющегося при поглощении влаги из воздуха. С легкоокисляющимися веществами (порошок алюминия, сера, уголь и т. п.) перекись натрия реагирует настолько энергично, что взрыв может последовать иногда даже при простом соприкосновении реагирующих веществ [2].
Бертолетова соль также образует взрывчатые вещества в смеси с различными тонкоизмельченными порошками и органическими соединениями.
Эти обстоятельства в значительной мере обусловили постепенный отказ от использования сварочных генераторов с химическими методами получения кислорода.
Создание портативного сварочного аппарата с использованием кислорода, отбираемого из баллонов, также нецелесообразно. Перезарядка такого прибора кислородом связана с необходимостью применения сложных компримирующих устройств, что лишает прибор его основного достоинства — подвижности и независимости от базы.
В течение 1945—1948 гг. авторами были изготовлены и испытаны экспериментальные образцы химических сварочных генераторов, основанных на реакции каталитического разло¬жения высококонцентрированной перекиси водорода.
Концентрированная перекись водорода, бывшая несколько лет тому назад сравнительно редким продуктом, нашла в период второй мировой войны много новых областей применения.
Концентрированная перекись водорода представляет собой прозрачную бесцветную жидкость с очень слабым запахом. Удельный вес 90-%нoгo раствора перекиси водорода равен 1,393, вязкость —0,0130 пуаз при 18 С; температура замерзания 90% раствора равна —11 С; температура кипения (разложения) + 140 С.
Перекись водорода как источник получения кислорода для химического генератора имеет ряд преимуществ перед бертолетовой солью и перекисями щелочных металлов. Прежде всего, содержание активного кислорода в ней составляет 47%, т. е. значительно выше такового для других веществ. То, что перекись является жидкостью и может оставаться ею в водных растворах при температуре до —50 С, обеспечивает легкость ее подачи, простоту регулировки процесса и возможность произвольной его остановки.
Разложение перекиси водорода легко осуществляется с помощью катализаторов, причем в отличие от таких веществ, как Na2O4, происходит полностью и практически не зависит от температуры внешней среды.
Перекись водорода не взрывается при ударе и нагревании. Как показали специальные исследования [3], высококонцентрированная перекись водорода не детонирует под дей-ствием механических импульсов.
В отличие от бертолетовой соли перекись водорода не токсична, при попадании на кожу она вызывает лишь ее побеление и зуд, которые быстро проходят. Как известно, перекиси щелочных металлов вызывают тяжелые и труднозаживающие ожоги.
При концентрации до 65—70% перекись водорода не вызывает воспламенения тканей, дерева и т. п. При более высоких концентрациях воспламенение тканей может произойти только при наличии катализаторов. В отсутствии катализаторов, например при попадании на чистый хлопок или полированное дерево, даже 90%-мая перекись не вызывает их воспламенения.
В этом отношении стабилизованные водные растворы перекиси водорода выгодно отличаются от сжатого кислорода в баллонах, детонирующего под влиянием механических импульсов или загрязнений трубопроводов маслами и т. п., а также от перекисей щелочных металлов, воспламеняющих ткани, легко образующих взрывчатые смеси и неудобных в обращении.
Наконец, при хранении перекись водорода не может портиться в результате действия углекислого газа или влага воздуха. При хранении в алюминиевых баках, стоящих под открытым небом, потери перекиси составляют всего 1% в год [4]. Перекиси же металлов в течение года теряют до 20% активного кислорода [1].
По данным 1931 г. [5], стоимость 1 кг кислорода, получаемого ИЗ перекиси водорода, находилась в следующем соотношении со стоимостью кислорода, получаемого из других веществ:
Кислород из |
Условных единиц |
Н2О2 |
5 |
HNO3 |
3,6 |
К2Сг3О7 |
6,9 |
КClO3 |
1,5 |
KMnO4 |
2 |
Таким образом, в то время перекись водорода была дороже КМпО4 и КСlО3. Она также превосходила по стоимости и перекиси металлов, поскольку на реакции последних с кислотами был основан обычный метод ее получения, а электрическое получение щелочных металлов, предшествующее приготовлению их перекисей, является процессом энергоемким и дорогим.
Во время второй мировой войны положение коренным образом изменилось. К 1945 году более 50% всей мировой выработки перекиси водорода производилось из надсерной кислоты и ее солей в результате круговых процессов.
В настоящее время разработаны новые систематические и круговые способы получения перекиси водорода [6], освоено ее концентрирование и практически доказана высокая устойчивость чистой и стабилизованной перекиси водорода.
Концентрированная перекись водорода находит широкое применение в различных отраслях техники, например для регенерации отработанных кислот и других процессов.
УСТРОЙСТВО И РАБОТА КИСЛОРОДНОГО ГЕНЕРАТОРА
Пергидратный генератор кислорода (рис. 1) состоит из бачка 1, в котором хранится перекись водорода, регулятора 2, поддерживающего заданное давление и регулирующего подачу перекиси, реактора 3, где происходит каталитическое разложение перекиси, и змеевика-холодильника 4, соединенного тройником 5 с бачком 1. Вследствие такого соединения во всем аппарате поддерживается одинаковое давление, необходимое для стекания перекиси водорода в реактор.
Залитая в бачок 1 перекись водорода при открытии крана 7 через регулятор 2 стекает в реактор 3, где разлагается при соприкосновении с контактной сеткой 8.
Образующийся кислород через холодильник 4 идет в горелку, а остающаяся в реакторе вода по окончании работы сливается через кран 9.
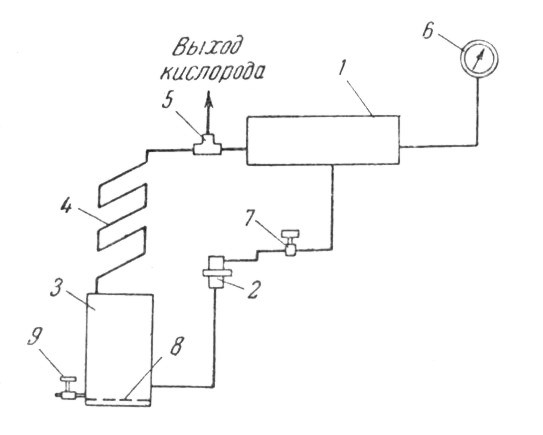
Рис. 1. Схема кислородного генератора: 1 — бак для хранения перекиси водорода; 2 — регулятор подачи перекиси водорода и давления кислорода в генераторе; 3— реактор каталитического разложения перекиси водорода; 4 — змеевик-холодильник; 5 — тройник; 6 — манометр; 7 — пусковой вентиль; 8 — серебряная контактная сетка; 9 — кран для слива воды.
Материал для изготовления генератора должен быть инертен по отношению к перекиси водорода и не должен окисляться ею. Как показала практика, наиболее подходящим материалом является алюминий высокой чистоты.
Бак 1 сделан сварным и рассчитан на давление до 10 атм. Объем бака — 0,4 — 2,5 л. Реактор 3 по конструкции аналогичен баку 1, причем объем его составляет 0,8 от объема последнего. В нижней части реактора имеется горловина, завинчивающаяся крышкой, на которой укреплена серебряная контактная сетка (0,5—1,0 г). Вместо серебра в качестве катализатора могут быть использованы двуокись марганца, окись железа и др.
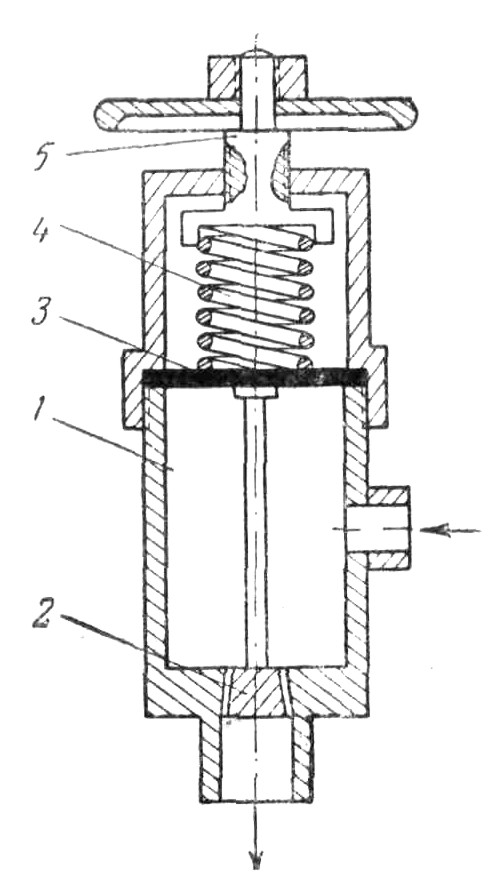
Рис. 2. Регулятор давления кислородного генератора: 1 — корпус регулятора; 2 — клапан подачи перекиси водорода; 3 — мембрана регулятора; 4— пружина регулятора; 5 — винт регулятора давления.
Дозировка количества подаваемого кислорода производится краном горелки. Давление автоматически поддерживается постоянным посредством регулятора (рис. 2). После того как будет открыт пусковой вентиль, перекись начнет поступать в корпус 1 регулятора и через зазор клапана 2 в реактор. При повышении давления в реакторе повышается давление и в заливном бачке, а следовательно, и давление перекиси, поступающей в регулятор подачи.
Мембрана 3 при этом прогибается, сжимая пружину 4, и при определенном давлении клапан 2 закрывается. Уменьшение давления в реакторе при расходе кислорода приводит к тому, что открывается клапан 2, после чего перекись снова начинает поступать в реактор.
При установившемся режиме работы мембрана занимает некоторое среднее положение; давление при котором это произойдет, определяется жесткостью пружины 4. Вращая винт 5 и наблюдая за показаниями манометра, можно установить любое необходимое давление.
Вес бака и реактора, изготовленных из алюминия толщиной 4 мм при объеме в 1,5 л, составляет около 1,0 кг. Столько же весят манометр, регулятор подачи, краны, змеевик; общий вес пустого кислородного генератора составляет 2,0—2,5 кг. При объеме бака в 0,9 л и коэффициенте заполнения 0,9 одновременно может быть залито около 1,0 кг 80-%ного водного раствора перекиси водорода, что соответствует 270 л кислорода.
Экспериментальные образцы кислородного генератора были испытаны в условиях эксплуатации. Последний из образцов (рис. 3) был выполнен из меди, полужен изнутри и хромирован снаружи. Рабочее давление составляло 2—3 атм и устанавливалось спустя 3—4 секунды после открытия пускового вентиля. Температура получаемого кислорода при длине отводящего шланга в 5 м и более не превышала 25 С (при внешней температуре в 18— 20 С).
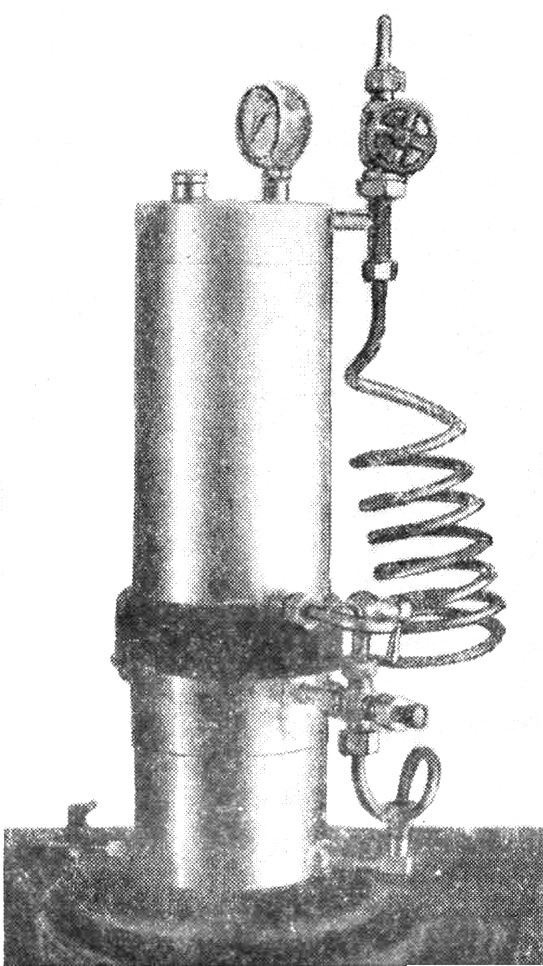
Рис. 3. Экспериментальный образец кислородного генератора.
При резке, в связи с увеличением расхода кислорода, температура кислорода значительно повышалась (до 120—130 С), а содержание влаги доходило до 15%. Поэтому в последнем образце кислородного генератора был дополнительно смонтирован осушительный патрон, заполненный крупнозернистым силикагелем марки «КСК» с коэффициентом поглощения 0,8. Патрон содержал 1,2 кг силикагеля и работал 3—4 зарядки, после чего производилась его регенерация нагреванием до 150—1800 С.
УСТРОЙСТВО И РАБОТА КОМБИНИРОВАННОГО СВАРОЧНОГО ГЕНЕРАТОРА
Сварка на кислороде, полученном из химических веществ, дороже обычной, поэтому область ее применения ограничивается условиями, окупающими эту дороговизну. В качестве горючих газов наиболее правильным является применение паров жидких горючих: бензина, бензола, керосина и т. п.
Как уже указывалось, в простейшем случае можно механически сочетать описанный выше кислородный генератор с существующими бензобачками. Однако некоторые особенности перекиси водорода позволяют сконструировать комплексный газосварочный генератор с оригинальным способом подачи горючего.
При разложении перекиси водорода выделяется около 700 ккал/кг тепла, т. е. 2 ккал на 1 л кислорода. Для нагревания 1 г бензина с 5 до 80 С с последующим испарением (удельная теплоемкость бензина 0,42, теплота парообразования 80) необходимо всего лишь 0,122 ккал, т. е. в 13 раз меньше. При резке количество выделенной теплоты еще больше превосходит энергию, необходимую для парообразования горючего. Поэтому при теплоотдаче через стенки аппарата температура в реакторе кислородного генератора достаточна для испарения и нагревания до 150—200 С нужного количества жидкого горючего.
Обычно жидкое горючее подается насосом в горелку, отличающуюся более сложным устройством и наличием в ней специального испарителя, подогреваемого отдельным пламенем или электроподогревом. Таким образом, испарение горючего происходит в самой горелке, что часто приводит к помехам в работе из-за засорения испарителя продуктами крекинга. Необходимо предъявлять особые требования к чистоте горючего, ибо в противном случае отверстия испарителя быстро засоряются и горелку приходится прочищать.
Зкзотермичность реакции разложения перекиси водорода позволяет устранить эти недостатки, осуществляя испарение горючего непосредственно в бачке за счет теплоты реакции.
Для этого бачок 1 с горючим (рис. 4) располагается отдельно от реактора 2 кислородного генератора. Реактор имеет цилиндрическую выемку, в которую вставляется испаритель 3. Внутренняя полость реактора отделена от горючего, находящегося в испарителе, двумя стенками, что гарантирует безопасность работы аппарата.
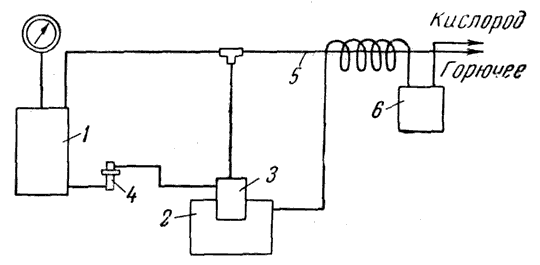
Рис. 4. Схема комбинированного аппарата для резки и сварки: 1 — бачок с горючим; 2 — кислородный генератор; 3—испаритель горючего; 4 — регулятор подачи жидкого горючего в испаритель; 5 — паропровод горючего; б — осушительный патрон.
Жидкое горючее поступает через регулятор подачи 4, аналогичный описанному выше регулятору пергидратного генератора. Паропровод 5 проходит внутри кислородного змеевика.
В кислородную магистраль включается осушительный патрон 6.
Преимущества такой схемы заключаются в следующем: 1) улучшается охлаждение кислородного реактора; 2) возможна работа на загрязненных и неочищенных сортах горючего; 3) устраняются неполадки в работе горелок, вызываемые оседанием в них продуктов крекинга.
При испытаниях этот комбинированный генератор продолжительное время работал на загрязненном горючем, которое оказалось непригодным для обычных горелок с испарителем.
ЛИТЕРАТУРА
1. Ходот В.В., Рудничные респираторы, 1948, стр. 50, Углетехиздат. 2. Некрасов Б.В., Курс общей химии, 1945, т. 2, стр. 631, Госхимиздат. 3. Физика и химия реактивного движения, 1949, сборник 1. 4. Химическая промышленность, 1947, № 7, стр. 28. 5. Техническая энциклопедия, т. 14, стр. 886. 6. Хомяков В.Г., Технология электрохимических производств, 1949, Госхимиздат.
|